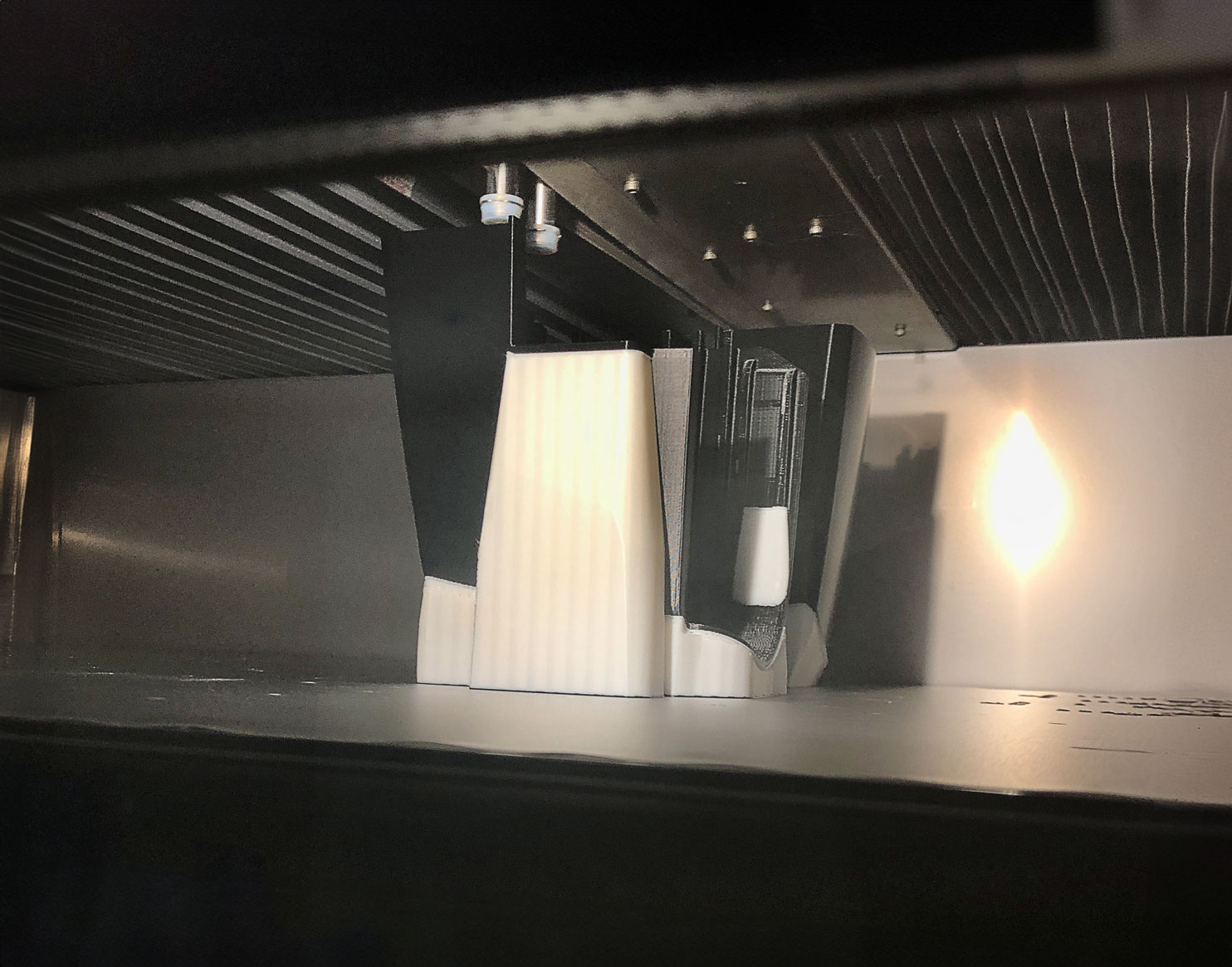
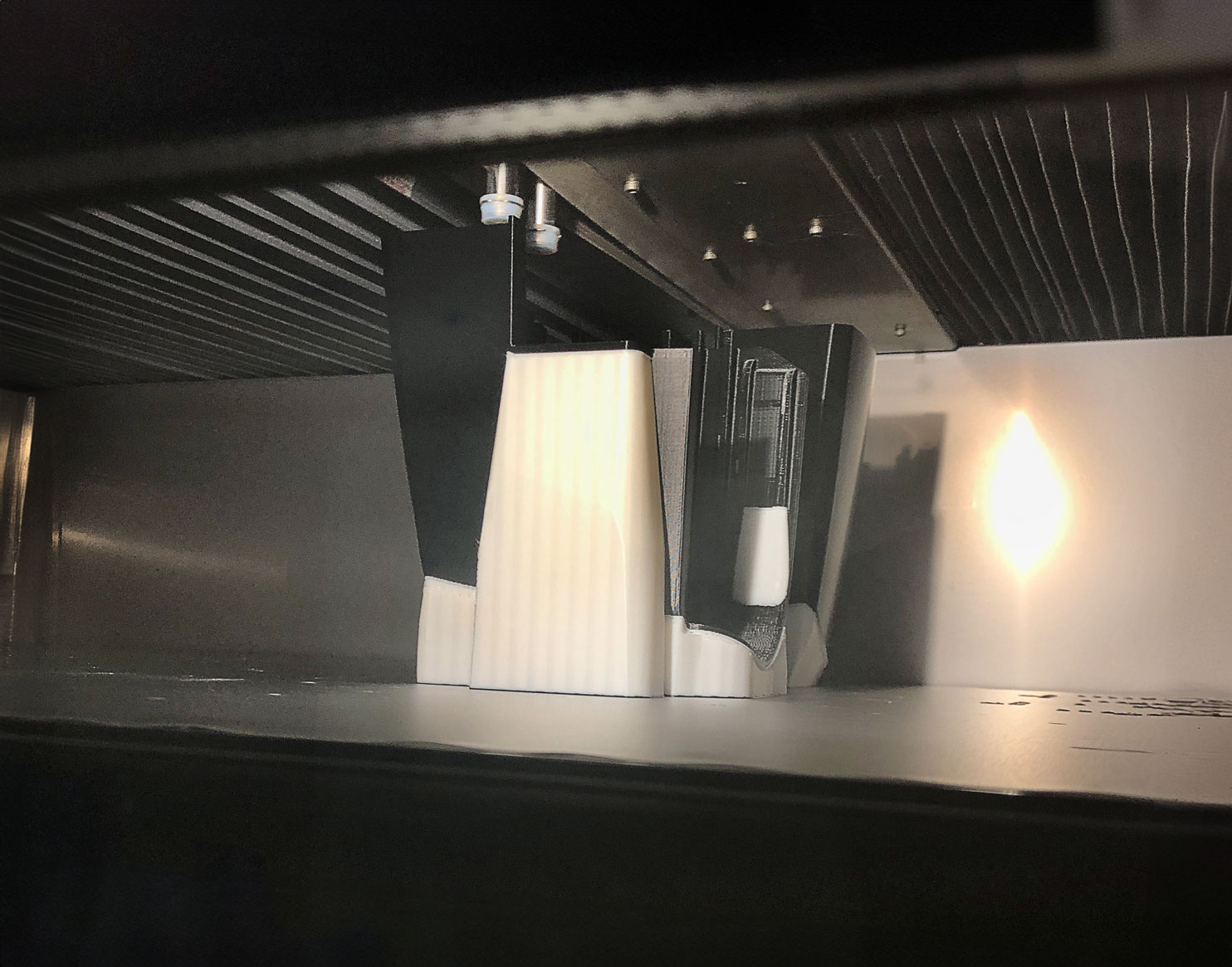
The automotive industry is experiencing an unprecedented revolution thanks to 3D printing, a technology that is radically transforming vehicle design, production, and assembly. In this article, we explore in detail the most exciting uses of 3D printing in the automotive sector, focusing on how this technology is redefining the very concept of the “car of the future.”
Performance Optimization and Weight Reduction
tridimensional printing offers enormous flexibility in the design and production of automotive components. With topological optimization, it’s possible to create lightweight and robust parts, reducing the vehicle’s overall weight. Here are some examples:
- Structural Components: Parts like frames, supports, and beams can be printed in advanced composite materials, offering greater strength and weight reduction compared to traditional solutions.
- Exhaust Systems: tridimensional printed exhaust manifolds can be designed to maximize airflow and reduce power loss.
- Suspensions: tridimensional printed bushings and spherical joints can improve vehicle handling and stability.
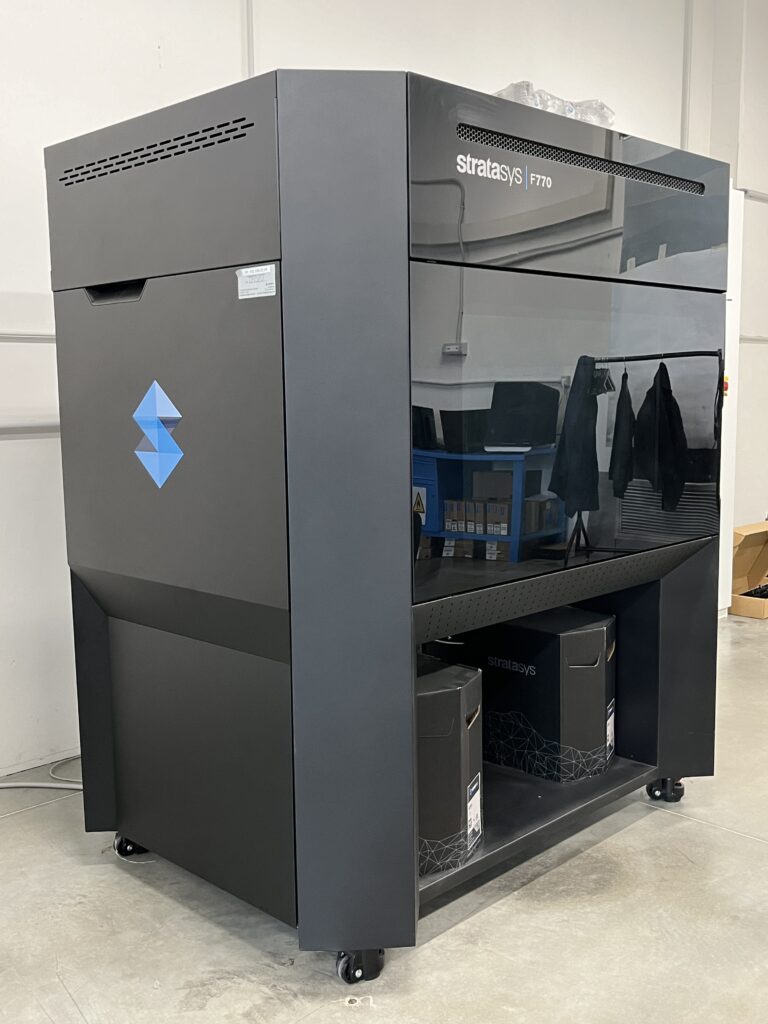
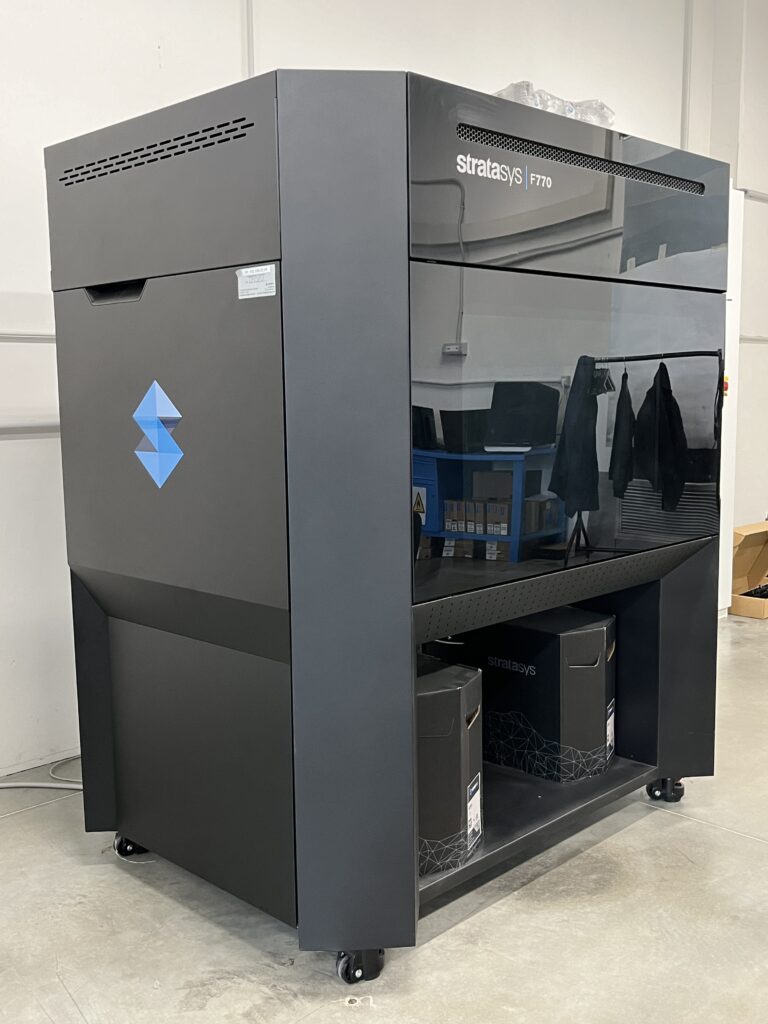
Customization and Unique Design
Tridimensional printing allows for unprecedented customization. Manufacturers can offer tailored interiors and accessories, creating a unique driving experience:
- Customized Interiors: Steering wheels, door panels, and center consoles can be designed and manufactured according to customer preferences.
- Unique Accessories: Tail lights with a specific “light signature,” custom emblems, and unique details can be precisely created.
Production of Parts and Components
Tridimensional printing is revolutionizing the production of automotive parts and components:
- Speed: Additive manufacturing allows for the rapid creation of complex parts, reducing development times.
- Mass Customization: On-demand production enables the creation of specific parts for each vehicle without the need for large component inventories.
Sustainability and Made in Italy
Additive manufacturing reduces material waste and resource usage. This is especially important for the automotive industry, which is increasingly embracing sustainability. Additionally, the “Made in Italy” label can be enhanced through local and customized component production.
Engineering Consulting and Rapid Prototyping
Fast Prototyping simplifies the creation of functional prototypes. Engineers can quickly test new solutions, accelerating the development process. Engineering consulting in the automotive sector can benefit from addictive manufacturing to develop innovative solutions.
In summary, addictive manufacturing is revolutionizing the automotive industry, offering advantages in terms of performance, customization, and sustainability. The future of cars will increasingly be shaped by this advanced technology.
What are the Main Challenges that Addictive Manufacturing Faces in the Automotive Industry?
While 3D printing offers significant advantages to the automotive industry, it also faces some challenges:
- Materials: Material selection is crucial. Mechanical properties, thermal resistance, and durability must meet automotive standards.
- Size and Scalability: addictive manufacturing is limited by machine size. Large-scale production requires scalability solutions.
- Production Speed: fast prototyping is slower compared to traditional methods. Optimizing production times is essential.
- Quality and Tolerances: Ensuring the precision and quality of printed parts is a challenge. Tolerances must be tight.
- Initial Costs and Expensive Materials: Investment in equipment and materials can be significant.
- Certifications and Regulations: Printed parts must comply with safety and quality regulations.
- Design for 3D Printing: Designing parts optimized for addictive manufacturing requires specific expertise.
Bieffe Project S.r.l. has extensive experience in addictive manufacturing and is therefore the ideal partner for the production of your components and spare parts. Here are a few examples:
- The door of a multi-material coupe supercar
- Components for the MMR Race Car Championship
- Motor Gallery: Excellence in Prototyping and addictive manufacturing
- Bieffe Project 3D Prototyping Lab
- Restomod and conversion of the engine from thermal to electric, and restyling with addictive manufacturing (video): Link to YouTube Video
In summary, the automotive industry is overcoming these challenges to fully harness the potential of addictive manufacturing.
The Bieffe Project 3D Prototyping Lab is equipped with extraordinary tools like the large-format Stratasys 770 printers, giving the lab enormous potential. Thanks to these advanced technologies, the lab can develop innovative solutions in the automotive engineering sector. Engineering consulting can benefit from addictive manufacturing, which is revolutionizing the automotive industry by offering superior performance, customization, and sustainability.
Despite the significant advantages, addictive manufacturing faces some challenges in the automotive sector. However, with the experience and expertise of Bieffe Project S.r.l., these challenges are overcome to fully exploit the potential of addictive manufacturing in the automotive industry.
WHO WE ARE AND WHAT WE DO
Bieffe Project is an engineering company specializing in automotive design, mechanical and industrial engineering, CAE, Design & Style, Manufacturing Technologies, Material Analysis, Rapid Prototyping/Modeling, and Composite Materials. Located in Modena, in the heart of the Motor Valley, the company has been active for over twenty years and boasts a prestigious clientele both nationally and internationally. We collaborate with the leading and most important automotive manufacturers, providing innovative and cutting-edge solutions, highly specialized technical support, and a strong sense of professionalism.
CONTACT US